The decarbonization of the agricultural equipment sector is well underway, and the agricultural sector will be no exception. Motivated by environmental concerns, the availability of oil in the medium term and a desire for energy independence, governments are encouraging manufacturers to offer alternatives to diesel. Several solutions are under development or already in use.
Hydrogen offers great potential
Already used in city buses and public transport, hydrogen has a major advantage: when in use, it emits only water into the atmosphere. It is used in two distinct technologies.
The first uses hydrogen fuel cells, an efficient principle which produces electricity that can be used on the vehicle, but is rather costly to develop. More and more automakers are therefore turning to the second solution, converting their engines to use hydrogen directly as a fuel.
Brands such as JCB offer handling tools that operate in this way. Hydrogen production is also becoming increasingly organized. This gas is not naturally present in the atmosphere, and needs to be synthesized from water and energy. Until now, manufacturers have generally used petroleum-based products in their manufacturing processes, but the sector has begun to transform itself to offer more and more "green" or decarbonated hydrogen, produced from renewable (solar, wind, etc.) or nuclear-generated electricity.
Engine failure?
The platform for diesel engine replacement solutions for agricultural, construction and industrial machinery.
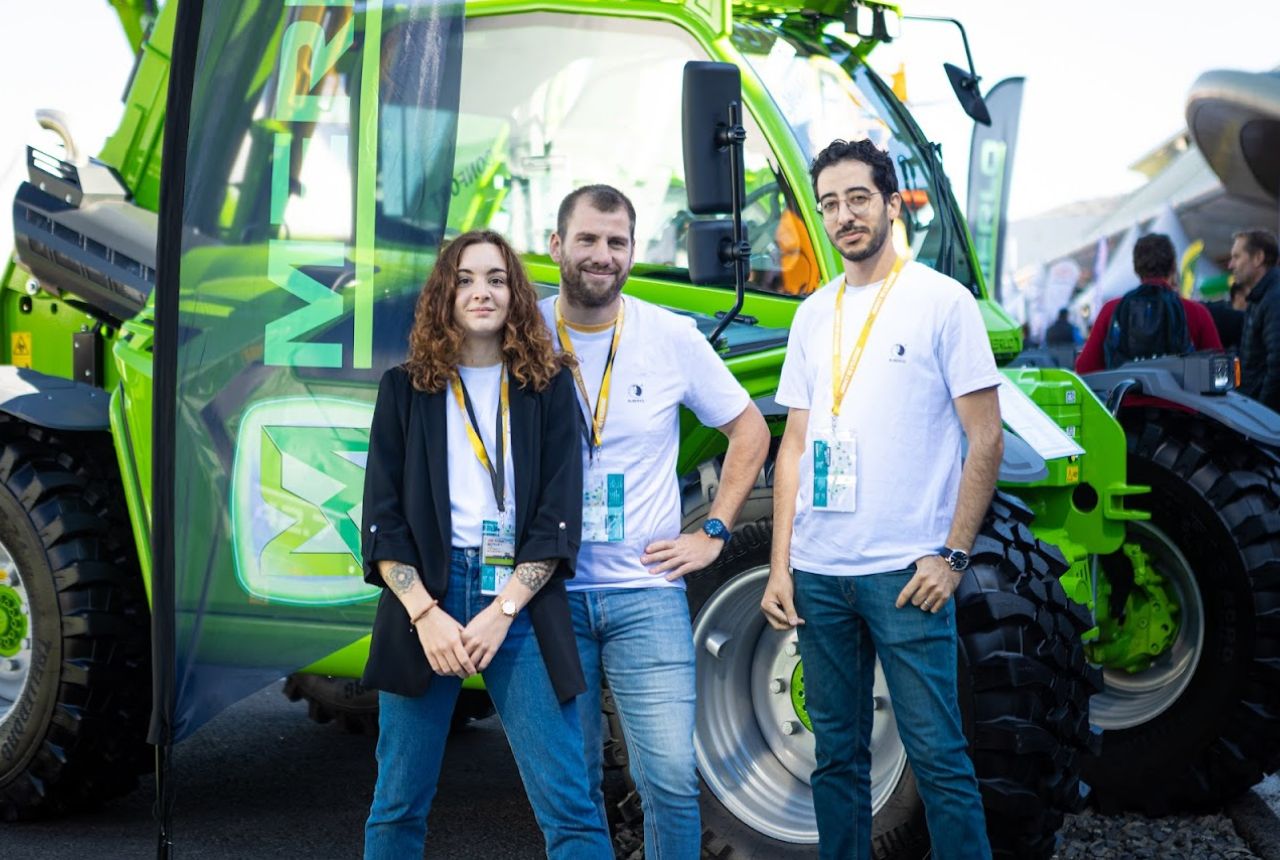
Biomethane: the advantage of on-farm production
Another promising avenue is the use of engines running on biomethane gas (or CH4), as promoted by NewHolland. For several years now, the brand has been offering a T6 180 (160 hp) tractor that runs on biomethane.
The advantage of this gas is that it is produced by methanization, enabling farmers with on-farm installations to convert their farm effluent into fuel. A fine example of the circular economy. Technically, this type of engine is just as efficient as a diesel model.
The main limitation is range. Even compressed methane is around five times bulkier than RNG. With the addition of a second tank, often placed at the front, the tractor can only work for 5 to 6 hours at full power. This may be sufficient for various uses, such as transport or light tillage. On the other hand, for long days in the field, a mobile refuelling solution should be considered.
Electricity is efficient at low power levels
Given their experience with forklift trucks, it was only logical that materials handling equipment manufacturers should be the first to offer 100% electric tools. Today, almost every brand has at least one battery-powered telescopic handler or articulated loader in its catalog.
For reasons of autonomy and performance, electric power is reserved for the smallest models in their ranges, while the more powerful versions are still powered solely by traditional diesel engines. However, with a range of 3 to 4 hours, an electric material handler can be used for a wide variety of farm applications. Tractor brands are also following suit, developing smaller models, from 50 to 100 hp, where the battery has replaced the combustion engine.
Electricity is also the energy source chosen by several manufacturers of agricultural robots commonly used in vineyards or market gardening.